Silicone Rubber Product Manufacturers
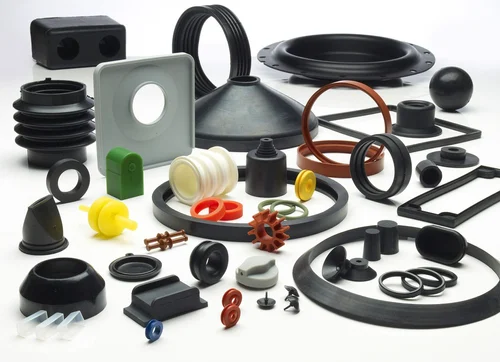
Contact : +91 97404 04503
Silicone Rubber Product Manufacturing
Silicone rubber, a versatile and durable material, is extensively used in various industries due to its unique properties such as flexibility, heat resistance, and chemical stability. The manufacturing process of silicone rubber products involves several critical stages to ensure the production of high-quality components suitable for diverse applications.
1. Material Preparation
The primary material for silicone rubber products is silicone, which is a polymer composed of silicon, oxygen, carbon, and hydrogen. The process begins with the preparation of silicone rubber compounds. Raw silicone polymers are mixed with various additives, such as fillers (e.g., silica), curing agents (crosslinkers), and pigments, to achieve desired properties. These additives are blended in precise proportions to ensure uniformity and consistency in the final product.
2. Mixing
The prepared silicone rubber compounds are subjected to a mixing process, often carried out in a banbury mixer or an internal mixer. This stage is crucial for achieving a homogeneous blend of the polymer and additives. The mixture is then cooled and often processed into sheets or pellets for ease of handling and subsequent use.
3. Molding and Shaping
Once the silicone rubber compound is prepared, it is formed into the desired shape through molding. There are several molding techniques, including:
-
Compression Molding: In this technique, the silicone compound is placed in a heated mold cavity. The mold is then compressed, forcing the compound into the mold's shape. This method is suitable for producing high-volume parts with simple geometries.
-
Injection Molding: Here, the silicone rubber compound is injected into a mold cavity under high pressure. This method is ideal for producing complex shapes and detailed parts with high precision.
-
Extrusion Molding: Silicone rubber is forced through a die to create long, continuous shapes, such as seals or gaskets. The extruded material is then cut into desired lengths.
4. Curing
The molded silicone rubber products undergo a curing process, also known as vulcanization. Curing involves heating the molded parts to a specific temperature for a defined period to initiate a chemical reaction that crosslinks the silicone polymers. This reaction transforms the silicone rubber from a soft, pliable state to a solid, elastic material. The curing process enhances the rubber’s mechanical properties, including its heat resistance, flexibility, and durability.
5. Post-Processing
After curing, the silicone rubber products are subjected to various post-processing steps to ensure they meet quality standards. This may include trimming excess material, inspecting for defects, and performing quality control tests. Additional finishing processes, such as painting, coating, or adding adhesives, may also be applied depending on the product’s requirements.
6. Quality Control
Quality control is a critical aspect of silicone rubber product manufacturing. Rigorous testing is conducted to verify that the products meet industry standards and specifications. Tests may include checking for tensile strength, elongation, hardness, and resistance to temperature, chemicals, and aging. Ensuring consistency and reliability in silicone rubber products is essential, particularly in applications requiring high performance and safety standards, such as in automotive, aerospace, medical, and industrial sectors.
7. Packaging and Distribution
Once the products pass quality control, they are packaged and prepared for distribution. Packaging methods vary based on the product’s nature and the customer’s requirements. Proper packaging is essential to protect the products from damage during transportation and handling.
In conclusion, the manufacturing of silicone rubber products is a sophisticated process involving precise material preparation, molding, curing, and quality control. The resulting products are valued for their durability, flexibility, and resistance to extreme conditions, making them suitable for a wide range of industrial and commercial applications.