Silicon Rubber Products Manufacturer
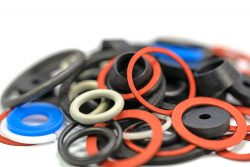
Contact : +91 97404 04503
Manufacture of Silicon Rubber Products
Silicon rubber, renowned for its high-performance characteristics, is a critical material used across various industries. The manufacture of silicon rubber products involves a sophisticated process that ensures the material’s unique properties are preserved and optimized for end-use applications. This process generally includes formulation, molding, curing, and finishing stages.
1. Formulation
The manufacturing process begins with the formulation of the silicon rubber compound. Silicon rubber is primarily composed of silicon, oxygen, carbon, and hydrogen. The base material is a silicon polymer, often in the form of a liquid or gel, which is mixed with various additives to enhance its properties. These additives include fillers (like silica or carbon black) to improve strength and durability, curing agents (like peroxides or platinum catalysts) to facilitate the cross-linking process, and other modifiers to adjust flexibility, hardness, or color.
The formulation stage is crucial as it determines the final properties of the silicon rubber. The mixing of these components is done in a controlled environment to ensure uniform distribution and prevent contamination. This process is typically carried out in high-precision equipment like sigma mixers or extruders.
2. Molding
Once the formulation is complete, the silicon rubber compound is shaped into products through various molding techniques. The most common molding processes include:
-
Compression Molding: The rubber compound is placed in a heated mold cavity. Pressure is applied to force the compound to conform to the mold’s shape. This method is suitable for making large and simple shapes.
-
Injection Molding: In this method, the rubber compound is injected into a mold under high pressure. This technique allows for high precision and is ideal for complex shapes and high-volume production.
-
Transfer Molding: Similar to compression molding, but the rubber is first preheated and then transferred into a mold cavity. This method helps reduce waste and is used for intricate parts.
-
Extrusion Molding: Silicon rubber is forced through a die to create continuous shapes like seals or gaskets. This process is often used for products that need to be cut into specific lengths.
3. Curing
Curing, or vulcanization, is a critical step in the manufacture of silicon rubber products. This process involves heating the rubber compound to facilitate cross-linking of the polymer chains. The curing agents added during the formulation stage react with the silicon polymers to form a three-dimensional network of bonds, which gives the silicon rubber its elasticity, strength, and durability.
The curing process can be conducted in various ways:
-
Heat Curing: The rubber is heated in an oven or autoclave, typically at temperatures ranging from 150°C to 200°C (302°F to 392°F). This method is commonly used for bulk curing.
-
Radiation Curing: This involves exposing the rubber to ultraviolet (UV) light or electron beams, which induces the cross-linking process. This method is often used for coatings or thin films.
4. Finishing
After curing, the silicon rubber products undergo finishing processes to meet quality and performance standards. These processes include:
-
Trimming and Cutting: Excess material from the molding process is trimmed away, and products are cut to specific sizes or shapes.
-
Surface Treatment: The surface of silicon rubber products may be treated to improve adhesion, enhance appearance, or provide additional functionality. This can include processes like plasma treatment or coating.
-
Quality Control: Rigorous testing is conducted to ensure that the products meet industry standards and specifications. Tests may include mechanical property assessments, thermal stability tests, and chemical resistance evaluations.
5. Packaging and Distribution
Finally, the finished silicon rubber products are packaged for distribution. Packaging is designed to protect the products during transportation and storage. Proper labeling and documentation are also crucial for ensuring traceability and compliance with regulatory requirements.
In summary, the manufacture of silicon rubber products involves a detailed and controlled process, from formulation and molding to curing and finishing. Each stage is designed to enhance the material’s inherent properties, ensuring that the final products meet the high performance and durability standards required by various industries.