Rubber Seals Manufacturer
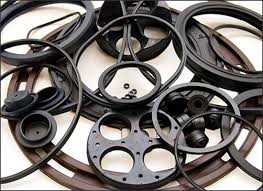
Contact : +91 97404 04503
Rubber Seals Manufacturing
Rubber seals are essential components used in various industries for preventing leaks, reducing friction, and enhancing product durability. These seals are typically placed between two surfaces to prevent the passage of gases or liquids. Industries like automotive, aerospace, construction, and even household appliances rely heavily on rubber seals to ensure the smooth functioning of equipment. In this article, we explore the process of rubber seals manufacturing, types of rubber seals, and their wide range of applications.
Types of Rubber Seals
-
O-Rings: One of the most commonly used rubber seals, O-rings, are donut-shaped seals used to prevent the leakage of fluids. They are typically found in engines, pumps, and pipelines.
-
Gaskets: Gaskets are flat, often circular or oval, seals that can fit between two surfaces to prevent leakage of fluids. They are frequently used in automotive engines and mechanical systems.
-
Lip Seals: Lip seals are designed to protect machinery by keeping lubricants in and contaminants out. They are used in equipment like bearings and motors.
-
Custom Seals: Many industries require seals that are custom-made to fit unique specifications, particularly in specialized machinery and equipment.
Rubber Seals Manufacturing Process
The process of manufacturing rubber seals involves several key steps, ensuring precision and quality in every seal produced:
-
Material Selection: Rubber seals can be made from various types of rubber, including natural rubber, nitrile rubber, silicone rubber, EPDM, and Viton. The selection of the material depends on the specific application and environmental conditions like temperature, pressure, and exposure to chemicals.
-
Rubber Compounding: After selecting the material, rubber is mixed with additives such as accelerators, fillers, and stabilizers to enhance its properties. This process, known as compounding, helps improve the seal's durability, resistance to heat, and elasticity.
-
Molding: The mixed rubber is then shaped using different molding techniques:
- Compression Molding: The rubber is placed into a mold, and heat and pressure are applied to form the seal.
- Injection Molding: The rubber is injected into a mold cavity at high pressure and then allowed to cool and solidify.
- Transfer Molding: In this method, the rubber is transferred into a mold cavity under pressure to create seals with complex shapes.
-
Curing/Vulcanization: Once the rubber has been molded, it is subjected to the process of vulcanization, which involves heating the material to strengthen its structure. This ensures the rubber maintains its shape, resists wear and tear, and can withstand the rigors of its intended application.
-
Post-Processing: After curing, the rubber seals are trimmed, inspected, and, if necessary, coated for additional durability. This step ensures that the seals meet the required specifications for quality and precision.
Applications of Rubber Seals
Rubber seals have a wide range of applications across multiple industries:
-
Automotive: Used in engines, transmissions, brakes, and suspension systems to prevent fluid leaks and maintain mechanical integrity.
-
Aerospace: Critical for ensuring the safety of aircraft systems by preventing leaks in fuel systems and hydraulic systems.
-
Industrial Machinery: Rubber seals are essential in pumps, valves, compressors, and gearboxes to prevent leaks and enhance the longevity of mechanical components.
-
Oil and Gas: Rubber seals are used to prevent leaks in pipelines, drilling equipment, and refineries, making them a crucial component in the oil and gas industry.
-
Home Appliances: From washing machines to refrigerators, rubber seals are used in household appliances to ensure smooth operation and prevent water or gas leaks.
Conclusion
Rubber seals manufacturing is a sophisticated process that requires attention to material selection, molding techniques, and post-processing to produce high-quality seals. These seals play a vital role in various industries, contributing to safety, efficiency, and product longevity. By understanding the manufacturing process and the importance of rubber seals, businesses can choose the right seals for their applications, ensuring optimal performance and durability.
Whether in automotive engines, aerospace equipment, or household appliances, rubber seals are the unseen heroes that prevent leaks and maintain mechanical integrity, making them indispensable in today's technology-driven world.