Rubber Profiles and Cords Manufacturer
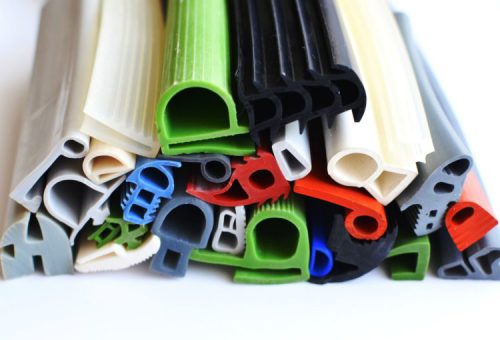
Rubber Profiles and Cords Manufacture
The manufacture of rubber profiles and cords is a specialized process within the rubber industry, catering to a variety of applications across different sectors. Rubber profiles and cords are essential components used in construction, automotive, aerospace, and industrial applications, among others. The production process involves several stages, each crucial for ensuring the quality and performance of the final product.
1. Material Selection:
The production of rubber profiles and cords begins with the selection of appropriate rubber compounds. These compounds are typically composed of natural rubber or synthetic rubbers such as neoprene, nitrile, silicone, or EPDM (ethylene propylene diene monomer). The choice of rubber depends on the desired properties of the final product, including flexibility, durability, resistance to temperature extremes, and chemical resistance.
2. Mixing:
Once the rubber compound is selected, the raw materials are mixed together in a process known as mastication. This involves blending rubber with various additives, such as fillers, vulcanizing agents, and stabilizers, in a large mixer. The goal is to achieve a uniform and homogeneous mixture that will provide the desired properties in the finished rubber profiles and cords.
3. Extrusion:
The next step in the manufacturing process is extrusion. The rubber mixture is fed into an extruder, a machine that forces the rubber through a mold to create continuous profiles or cords of the desired shape and size. Extrusion allows for precise control over the dimensions of the rubber profiles, which is critical for ensuring consistency and accuracy in the final product.
4. Vulcanization:
After extrusion, the rubber profiles and cords undergo a curing process known as vulcanization. This involves heating the rubber to a specific temperature in the presence of sulfur or other curing agents. Vulcanization cross-links the rubber molecules, enhancing the material's elasticity, strength, and durability. The result is a more robust and resilient rubber profile or cord that can withstand various stresses and environmental conditions.
5. Cutting and Shaping:
Once vulcanization is complete, the continuous rubber profiles and cords are cooled and cut to the required lengths or shapes. This step may involve cutting the profiles into specific sizes for use in different applications or shaping them to fit particular design specifications. Precision in cutting and shaping is essential to ensure that the rubber components meet the required tolerances and performance standards.
6. Quality Control:
Quality control is a critical aspect of the manufacturing process for rubber profiles and cords. Rigorous testing is conducted to assess the physical and mechanical properties of the rubber, including tensile strength, elongation, hardness, and resistance to wear and tear. Additionally, the rubber profiles are inspected for any defects, such as bubbles, cracks, or inconsistencies, to ensure that they meet the required quality standards.
7. Packaging and Distribution:
Once the rubber profiles and cords pass quality control, they are packaged for distribution. Proper packaging is essential to protect the products during transportation and storage. The packaging may include labeling with product information, handling instructions, and specifications. The final products are then distributed to various industries and customers, ready for use in their respective applications.
Conclusion:
The manufacture of rubber profiles and cords involves a complex and carefully controlled process to produce high-quality components for a wide range of applications. From material selection and mixing to extrusion, vulcanization, and quality control, each stage of the production process plays a vital role in ensuring the performance and reliability of the finished products. As industries continue to evolve and demand more specialized rubber components, advancements in manufacturing techniques and materials will drive further innovations in the production of rubber profiles and cords.