Rubber Product Manufacturers in Gujarat
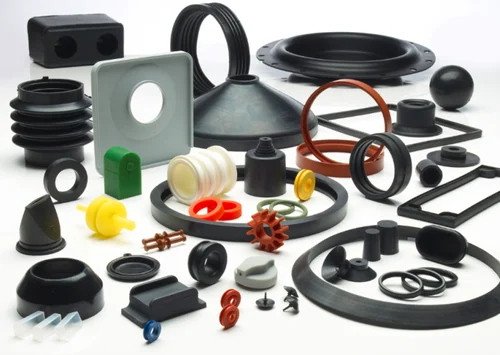
Contact : +91 97404 04503
Rubber product manufacturing plays a critical role in a wide range of industries, providing essential components for everything from automotive parts to medical devices. The process of rubber product manufacturing involves several stages, from raw material preparation to the final product, using various methods to shape and refine the material. This sector has seen significant growth due to increased demand in industries such as automotive, healthcare, and construction.
Key Processes in Rubber Product Manufacturing
-
Compounding: The rubber manufacturing process begins with compounding, where raw rubber is mixed with additives such as fillers, accelerators, and plasticizers. This step ensures that the rubber has the desired physical properties, such as strength, flexibility, and durability. The compound is crucial as it determines the performance of the final rubber product.
-
Molding and Shaping: After compounding, the rubber is shaped using various molding techniques. The most common methods include compression molding, transfer molding, and injection molding. These processes involve placing the rubber compound into a mold, where it is heated and pressurized to take the shape of the desired product. Each molding technique has its own advantages and is chosen based on the complexity, size, and type of product.
-
Curing (Vulcanization): Vulcanization is a critical step in rubber product manufacturing. It involves heating the rubber with sulfur to improve elasticity, durability, and heat resistance. This chemical process creates cross-links between the rubber molecules, transforming it into a more stable material suitable for industrial use. Depending on the application, manufacturers may modify the vulcanization process to achieve specific properties.
-
Finishing and Quality Control: Once the rubber product is molded and cured, it undergoes finishing processes like trimming, deburring, and surface treatment. These steps ensure the product meets specific tolerances and standards. Quality control is crucial in rubber product manufacturing, as products must meet precise specifications for performance, safety, and longevity. Testing methods include tensile strength tests, hardness measurements, and heat resistance assessments.
Applications of Rubber Products
Rubber products are essential in numerous industries, including:
-
Automotive: Rubber components such as tires, seals, gaskets, and hoses are vital for the functioning of vehicles. These products must withstand extreme temperatures, pressure, and wear.
-
Medical: In healthcare, rubber is used to manufacture gloves, tubing, catheters, and seals. These products must adhere to strict standards of safety, biocompatibility, and sterility.
-
Construction: Rubber materials like weatherstripping, flooring, and roofing membranes are common in construction, providing insulation, durability, and water resistance.
-
Consumer Goods: Everyday products like footwear, sporting equipment, and household items often contain rubber components due to their flexibility and resilience.
Future Trends in Rubber Manufacturing
Sustainability is becoming a key trend in the rubber manufacturing industry. Manufacturers are focusing on eco-friendly processes, such as recycling rubber and using renewable raw materials. Innovations in rubber compounding, including the development of bio-based rubber, are helping to reduce the industry’s environmental footprint.
Automation and smart manufacturing are also gaining momentum. The integration of robotics, AI, and IoT technologies into rubber production is enhancing precision, efficiency, and quality control, leading to reduced waste and faster production times.
Conclusion
Rubber product manufacturing is a vital industry with diverse applications across various sectors. Advances in materials science, coupled with a growing emphasis on sustainability, are driving innovation in this field. Whether used in automobiles, healthcare, or construction, rubber products continue to play an essential role in modern industrial processes, ensuring durability, flexibility, and reliability.