Rubber Part Manufacturing
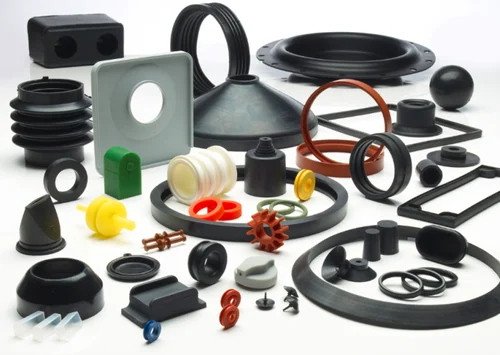
Contact : +91 97404 04503
The Essentials of Rubber Part Manufacturing
Introduction to Rubber Part Manufacturing
Rubber part manufacturing is a critical sector within the industrial landscape, serving as the backbone for numerous applications across various industries. This process involves the creation of rubber components that are integral to the functionality and performance of a wide range of products. From automotive parts and consumer goods to medical devices and industrial machinery, rubber parts are essential due to their durability, flexibility, and resistance to wear and tear.
Key Processes in Rubber Part Manufacturing
-
Compounding: The rubber manufacturing process begins with compounding, where raw rubber is mixed with various additives to enhance its properties. This mixture typically includes curing agents, fillers, plasticizers, and other chemicals that improve the rubber’s strength, flexibility, and longevity. The goal is to create a rubber compound that meets the specific requirements of the final product.
-
Molding: Once the rubber compound is prepared, the next step is molding. This can be achieved through various techniques such as compression molding, injection molding, and transfer molding. Each method has its advantages depending on the complexity and volume of the parts being produced:
- Compression Molding: Ideal for large, simple parts, this method involves placing the rubber compound into a mold cavity and applying heat and pressure to shape the material.
- Injection Molding: This technique is used for more complex parts. The rubber compound is injected into a heated mold under high pressure, ensuring precise and consistent shapes.
- Transfer Molding: A hybrid of compression and injection molding, this method involves transferring the rubber from a preheated chamber into a mold cavity, offering a balance between quality and efficiency.
-
Curing: Curing, or vulcanization, is a crucial step where the rubber is heated to form cross-links between the polymer chains. This process enhances the rubber’s strength, elasticity, and resistance to environmental factors. Curing can be done using different methods such as sulfur vulcanization or peroxide curing, depending on the desired properties of the rubber.
-
Finishing: After curing, the rubber parts undergo finishing processes to meet the required specifications. This may include trimming excess material, surface treatments, or additional quality checks. Finishing ensures that the parts are free from defects and ready for use.
Applications of Rubber Parts
Rubber parts find applications across various industries due to their versatility:
- Automotive Industry: Rubber components such as gaskets, seals, and hoses are essential for vehicle performance and durability.
- Consumer Goods: Items like rubber bands, grips, and seals are common in everyday products.
- Medical Devices: Rubber parts are used in medical equipment due to their biocompatibility and flexibility.
- Industrial Machinery: Rubber components are employed in machinery for vibration isolation, sealing, and shock absorption.
Quality Control and Standards
Quality control is a vital aspect of rubber part manufacturing. Manufacturers must adhere to industry standards and regulations to ensure the reliability and safety of their products. This involves rigorous testing for mechanical properties, chemical resistance, and durability. Certifications such as ISO 9001 can indicate a manufacturer’s commitment to quality and consistency.
Conclusion
Rubber part manufacturing is a sophisticated process that combines material science with precision engineering to produce components essential for a variety of applications. By understanding the key processes—compounding, molding, curing, and finishing—businesses can optimize their production methods and ensure high-quality products. Whether for automotive, consumer, medical, or industrial use, rubber parts play a pivotal role in modern technology and industry.