Rubber Hose Manufacturers
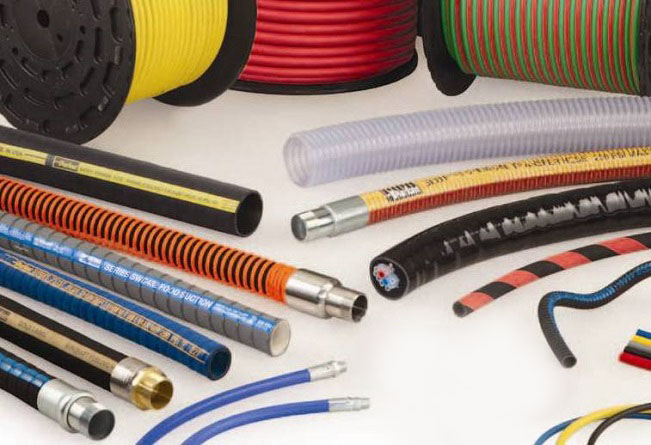
Rubber hose manufacturing is a specialized industry focused on producing durable, flexible hoses used across a wide range of applications. These hoses are integral components in various sectors, including automotive, industrial, aerospace, and consumer products. The process of manufacturing rubber hoses involves several key stages, from the selection of raw materials to the final quality testing of the finished product.
Raw Materials and Formulation
The production of rubber hoses begins with the selection of high-quality raw materials. The primary ingredient is rubber, which can be natural or synthetic. Natural rubber is derived from the latex of rubber trees, while synthetic rubbers are manufactured from petrochemicals. Common types of synthetic rubber used include nitrile, neoprene, and EPDM, each chosen for their specific properties such as resistance to oil, heat, or chemicals.
The rubber compound is formulated by mixing the base rubber with various additives, including fillers, curing agents, and stabilizers. Fillers like carbon black or silica are added to enhance the strength and durability of the hose. Curing agents, such as sulfur, are used in a process called vulcanization to cross-link the rubber molecules, providing the hose with its final elasticity and resilience.
Hose Construction
Once the rubber compound is prepared, the manufacturing process involves several steps:
-
Extrusion: The rubber compound is fed into an extruder, a machine that shapes the rubber into a continuous tube. The extruder heats the rubber and forces it through a die to form the desired hose shape. The extrusion process determines the hose's inner and outer diameters and wall thickness.
-
Reinforcement: To enhance the strength and pressure resistance of the hose, reinforcement layers are added. These layers can be made from various materials, including textile fabrics, steel wires, or synthetic fibers. The reinforcement is embedded in the hose either during the extrusion process or through a subsequent winding process. For example, textile braiding is commonly used to provide flexibility and resistance to abrasion.
-
Curing/Vulcanization: After the hose is extruded and reinforced, it undergoes curing or vulcanization. This process involves heating the hose in an autoclave or oven to cross-link the rubber molecules, which improves the hose’s strength, elasticity, and heat resistance. The vulcanization process also solidifies the rubber, giving the hose its final properties.
-
Finishing: Once vulcanized, the hose is cooled and undergoes finishing processes such as cutting to length, applying end fittings, or adding protective coatings. End fittings can be crimped or bonded to the hose, depending on the design requirements. The protective coatings, often made from synthetic polymers or fabric, help to improve the hose’s resistance to environmental factors such as UV radiation, abrasion, and chemicals.
Quality Control and Testing
Quality control is a crucial aspect of rubber hose manufacturing. The finished hoses undergo rigorous testing to ensure they meet industry standards and performance specifications. Tests may include pressure testing, flexibility testing, abrasion resistance, and chemical compatibility tests. Quality control measures are in place throughout the manufacturing process to detect any defects or inconsistencies early on.
Applications and Market Trends
Rubber hoses are used in a wide array of applications, including hydraulic systems, fuel delivery, air and water transfer, and industrial processes. The demand for rubber hoses is driven by advancements in technology and the growth of industries such as automotive, construction, and aerospace.
Recent trends in the rubber hose industry include the development of hoses with enhanced performance characteristics, such as improved temperature resistance, reduced weight, and increased flexibility. Additionally, there is a growing emphasis on sustainability, with manufacturers exploring eco-friendly materials and recycling options.
In summary, rubber hose manufacturing is a complex process that involves careful selection of materials, precise construction techniques, and rigorous quality control. The resulting hoses play a critical role in numerous applications, making them essential components in modern industry and everyday life.