Rubber Flooring Mat Manufacturer
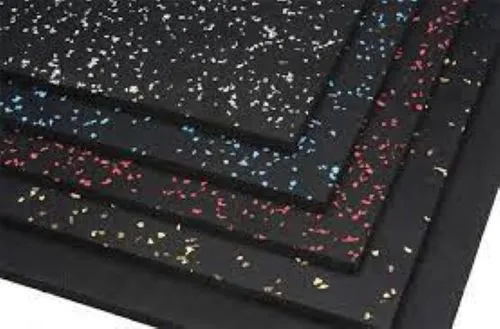
Rubber flooring mats have become increasingly popular across various industries, from fitness centers and sports facilities to commercial and residential spaces. They offer a versatile, durable, and safe solution for flooring needs, making them a preferred choice for many. The manufacturing process of rubber flooring mats is a sophisticated one, requiring a blend of technology, precision, and high-quality raw materials.
Raw Materials
The primary raw material used in the production of rubber flooring mats is natural or synthetic rubber. Natural rubber is derived from latex, a milky fluid found in rubber trees, while synthetic rubber is produced from petroleum-based chemicals. Recycled rubber, often sourced from discarded tires, is also commonly used in the production of rubber mats, contributing to environmental sustainability.
In addition to rubber, other materials like fillers, pigments, stabilizers, and processing aids are added to enhance the properties of the final product. Fillers like carbon black or silica improve the strength and durability of the mats, while pigments are used to add color. Stabilizers help in maintaining the chemical stability of the rubber, especially under conditions of heat and UV exposure.
Manufacturing Process
The manufacturing process of rubber flooring mats can be broadly categorized into the following stages:
-
Mixing: The first stage in the production process is mixing the raw materials. Rubber, along with fillers, pigments, and other additives, is blended in large mixers to create a homogeneous compound. This process ensures that all the ingredients are uniformly distributed, which is crucial for the consistency and quality of the final product.
-
Molding: Once the rubber compound is ready, it is shaped into mats through a molding process. There are different molding techniques used, including compression molding, injection molding, and transfer molding. In compression molding, the rubber compound is placed in a mold and then subjected to high pressure and heat, causing it to take the shape of the mold. Injection molding involves injecting the rubber compound into a mold cavity under high pressure, which is then heated to cure the rubber.
-
Curing: Curing is a vital step in the production of rubber mats. During this process, the rubber compound undergoes a chemical reaction known as vulcanization, which cross-links the polymer chains in the rubber, enhancing its elasticity, strength, and durability. The curing process typically occurs under controlled temperature and pressure conditions in a vulcanizing oven.
-
Finishing: After curing, the mats are removed from the molds and undergo finishing processes. This can include trimming excess material, surface texturing, or adding any special coatings. Surface texturing, such as diamond or coin patterns, can be applied to improve the grip and aesthetic appeal of the mats.
-
Quality Control: Quality control is an essential part of the manufacturing process. Rubber flooring mats are subjected to various tests to ensure they meet the required standards for durability, safety, and performance. Tests can include hardness testing, tensile strength, slip resistance, and fire retardancy.
-
Packaging and Distribution: Once the mats pass the quality checks, they are cleaned, packaged, and prepared for distribution. Packaging is done in a way that protects the mats during transportation and storage.
Environmental Considerations
The production of rubber flooring mats has an environmental impact, but manufacturers are increasingly adopting sustainable practices. The use of recycled rubber is one such measure, reducing the demand for raw materials and diverting waste from landfills. Additionally, many manufacturers are now implementing energy-efficient processes and reducing emissions during production.
Applications
Rubber flooring mats have a wide range of applications. They are commonly used in gyms and sports facilities due to their shock-absorbing properties, which protect both the flooring and the users. In industrial settings, rubber mats provide a non-slip surface that enhances safety. They are also popular in residential spaces, particularly in areas like kitchens, playrooms, and home gyms.
Conclusion
The manufacturing of rubber flooring mats is a complex process that combines advanced technology with careful material selection and environmental considerations. As demand for these versatile and durable flooring solutions continues to grow, manufacturers are likely to innovate further, offering even more sustainable and high-performance products to meet the needs of various industries.