Rubber Die Manufacturer
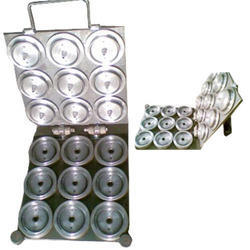
Rubber Die Manufacturing
Rubber die manufacturing is a specialized industry that plays a crucial role in various sectors, including automotive, electronics, and packaging. Rubber dies are used to create molds or stamps that shape rubber components and products. The manufacturing process of these dies requires precision, expertise, and advanced technology to ensure high-quality output. This article delves into the intricacies of rubber die manufacturing, exploring the process, applications, and innovations in the field.
The Rubber Die Manufacturing Process
-
Design and Prototyping
The first step in rubber die manufacturing involves designing the die. This process starts with understanding the specific requirements of the end product. Engineers and designers use Computer-Aided Design (CAD) software to create detailed blueprints of the die. The design includes all necessary dimensions, shapes, and features required to produce the desired rubber components.
Once the design is finalized, a prototype of the die is often created. This prototype helps in evaluating the design's functionality and making any necessary adjustments before moving to the final manufacturing stage.
-
Material Selection
Rubber dies are typically made from high-grade steel or aluminum alloys. The choice of material depends on factors such as the complexity of the die, the type of rubber to be processed, and the expected production volume. Steel is preferred for its durability and ability to withstand high pressures and temperatures, while aluminum is chosen for its lightweight properties and ease of machining.
-
Machining and Fabrication
With the design and material in place, the next step is machining and fabricating the die. This involves cutting, grinding, and shaping the die material to match the CAD design. Various machining processes, such as CNC milling, EDM (Electrical Discharge Machining), and surface grinding, are employed to achieve the required precision.
The machining process is critical as it determines the final quality of the die. Precision is essential to ensure that the die can produce rubber components with exact dimensions and surface finishes.
-
Heat Treatment
After machining, the die undergoes heat treatment to enhance its hardness and durability. Heat treatment processes such as annealing, quenching, and tempering are used to improve the mechanical properties of the die material. This step is crucial for ensuring that the die can withstand the stresses and strains involved in rubber molding.
-
Assembly and Testing
Once heat treatment is complete, the die components are assembled. This involves fitting together various parts of the die and ensuring that all components align correctly. The assembled die is then tested to verify its performance. This may involve trial runs with rubber material to check for any defects or inconsistencies.
Testing is an essential part of the manufacturing process as it helps identify any issues before the die is put into full-scale production. Any adjustments or refinements needed are made at this stage.
-
Finishing and Quality Control
The final step in rubber die manufacturing is finishing and quality control. This involves polishing the die to achieve a smooth surface and removing any burrs or imperfections. Quality control checks are conducted to ensure that the die meets all specifications and standards.
Rigorous inspection procedures are employed to verify the die's dimensions, surface finish, and overall functionality. Only after passing these checks is the die considered ready for use in production.
Applications of Rubber Dies
Rubber dies are used in a wide range of applications across various industries:
-
Automotive Industry
In the automotive industry, rubber dies are used to produce components such as gaskets, seals, and weather stripping. These components are essential for ensuring the proper functioning of vehicles and maintaining their performance and durability.
-
Electronics Industry
The electronics industry relies on rubber dies to manufacture components like rubber keypads, seals, and insulating materials. These components are crucial for protecting electronic devices from dust, moisture, and mechanical damage.
-
Packaging Industry
Rubber dies are also used in the packaging industry to create molds for various packaging materials. These molds help produce flexible packaging, such as rubberized seals and closures, that enhance the shelf life and safety of packaged goods.
-
Medical Industry
In the medical industry, rubber dies are used to produce components for medical devices and equipment. These components must meet strict quality and safety standards to ensure their reliability and effectiveness in medical applications.
Innovations in Rubber Die Manufacturing
The rubber die manufacturing industry is continually evolving, with advancements in technology and materials driving improvements in efficiency and quality. Some notable innovations include:
-
Advanced Materials
Researchers are developing new materials for rubber dies that offer enhanced properties such as increased hardness, wear resistance, and thermal stability. These advanced materials help extend the lifespan of dies and improve their performance.
-
Automation and Robotics
Automation and robotics are being increasingly integrated into the manufacturing process. Automated systems can perform repetitive tasks with high precision, reducing the risk of human error and increasing production efficiency.
-
3D Printing
3D printing technology is being explored for creating die prototypes and even final dies. This technology allows for rapid prototyping and complex designs that were previously difficult to achieve with traditional machining methods.
-
Enhanced Quality Control
Advanced inspection technologies, such as laser scanning and computer vision, are being used to enhance quality control procedures. These technologies provide more accurate and comprehensive assessments of die quality, ensuring that only the highest-quality dies are used in production.
Conclusion
Rubber die manufacturing is a complex and precise process that requires careful planning, expert craftsmanship, and advanced technology. From design and prototyping to machining and quality control, each step in the process plays a crucial role in ensuring the production of high-quality rubber components. As the industry continues to innovate and evolve, the future of rubber die manufacturing promises even greater advancements in efficiency, precision, and material performance.