Plastic Injection Moulding Companies In Bangalore
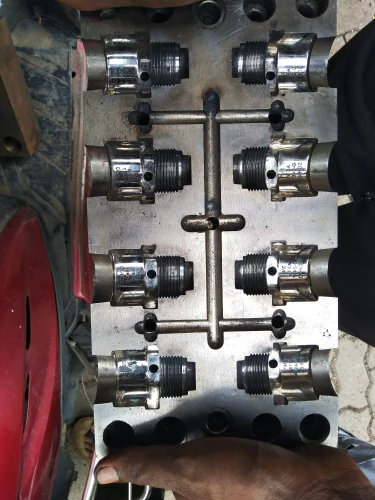
Plastic Injection Moulding: An Overview
Plastic injection moulding is a widely used manufacturing process for producing parts by injecting molten plastic material into a mould. This technique is highly efficient and versatile, enabling the creation of complex shapes with tight tolerances and high repeatability. It is a cornerstone of the plastic industry, used to create a wide range of products, from everyday consumer goods to high-performance industrial components.
The Process
The plastic injection moulding process begins with the preparation of plastic pellets, which are typically made from thermoplastics such as polyethylene, polypropylene, or polystyrene. These pellets are fed into a hopper, which directs them into a heated barrel. The plastic is then melted by heat and mechanical shear force in the barrel. Once melted, the plastic is injected under high pressure into a precisely designed mould cavity.
The mould itself is typically made from steel or aluminium and consists of two halves that are clamped together during the injection process. The molten plastic fills the cavity of the mould, taking the shape of the part. Once the material cools and solidifies, the mould opens, and the finished part is ejected. This process is repeated in a cycle, with each cycle producing one part. The speed and efficiency of the injection moulding process allow manufacturers to produce large quantities of identical parts with high precision.
Key Benefits
-
High Efficiency and Speed: Injection moulding is capable of producing parts in high volumes in a short amount of time. The process cycle time is typically very quick, making it ideal for mass production.
-
Complex Shapes: The ability to create intricate designs is one of the biggest advantages of plastic injection moulding. Moulds can be designed to produce parts with complex geometries, such as undercuts, holes, and threads.
-
Material Versatility: A wide range of thermoplastic materials can be used in injection moulding, including engineered plastics with special properties, such as heat resistance, electrical conductivity, and strength. This makes it suitable for a variety of industries, including automotive, electronics, medical, and consumer products.
-
Precision and Consistency: The high level of precision achieved in injection moulding ensures that parts are produced to exact specifications, with minimal variation from one part to another. This is particularly important in industries like aerospace and medical devices, where strict tolerances are required.
-
Low Labour Costs: Once the injection moulding machine is set up and the mould is prepared, the production process is largely automated, which reduces the need for extensive manual labor. This results in lower production costs over time.
Applications of Injection Moulding
Plastic injection moulding is used across numerous industries due to its flexibility and the wide range of materials that can be used. Common applications include:
- Consumer Goods: Toys, containers, kitchenware, and household items.
- Automotive: Dashboard components, bumpers, lighting housings, and under-the-hood parts.
- Electronics: Mobile phone cases, electrical connectors, and enclosures.
- Medical: Syringes, surgical instruments, and diagnostic devices.
Challenges and Considerations
Despite its many benefits, injection moulding does have some challenges. The initial cost of designing and producing the mould can be high, which makes it less ideal for small production runs. Additionally, the complexity of the mould design requires skilled engineering, and the process may not be cost-effective for low-volume production.
Conclusion
Plastic injection moulding is a cornerstone technology in the manufacturing sector, enabling the production of high-quality, complex parts at scale. Its versatility, speed, and precision make it an essential process for a variety of industries. While there are some challenges related to the cost of mould development and the need for expertise, the advantages it offers in terms of efficiency, material choice, and part complexity make it a preferred method for large-scale plastic part production.