Neoprene Rubber Products Manufacturer
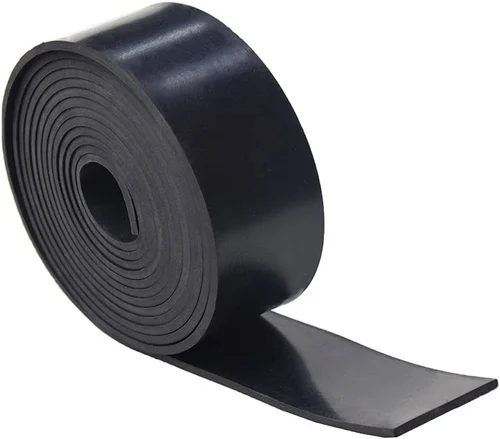
Contact : +91 97404 04503
Neoprene Rubber Products Manufacture
Neoprene rubber, also known as polychloroprene, is a versatile synthetic rubber used in a wide array of applications due to its unique properties. Manufactured through the polymerization of chloroprene, neoprene rubber exhibits excellent resistance to oil, chemicals, and environmental conditions. This makes it ideal for various industrial, automotive, and consumer product applications. The manufacturing process of neoprene rubber products involves several key steps, including polymerization, compounding, molding, and curing.
1. Polymerization
The production of neoprene rubber begins with the polymerization of chloroprene, a monomer that is obtained through the polymerization process. Chloroprene is polymerized using a variety of methods, including emulsion polymerization and bulk polymerization. In emulsion polymerization, chloroprene is dispersed in water with the help of emulsifiers and polymerized using a free-radical initiator. This method yields a latex form of neoprene, which is then coagulated to form rubber. Bulk polymerization, on the other hand, involves polymerizing chloroprene in the absence of a solvent, producing a solid form of neoprene rubber.
2. Compounding
Once the neoprene rubber is polymerized, it undergoes compounding. This process involves mixing the neoprene polymer with various additives to enhance its properties and suitability for specific applications. Common additives include fillers (such as carbon black or silica), plasticizers, stabilizers, curing agents (vulcanizing agents), and antioxidants. The purpose of these additives is to improve the rubber's physical properties, such as its strength, flexibility, and resistance to aging, heat, and ozone.
The compounding process is carried out using a rubber mill or an internal mixer, where the neoprene polymer and additives are thoroughly blended. The resulting compound is then shaped into sheets or other forms, depending on the intended end product.
3. Molding
The next step in the manufacture of neoprene rubber products is molding. During molding, the compounded neoprene rubber is shaped into the desired form using molds. This step can be achieved through various molding techniques, including compression molding, injection molding, and transfer molding.
-
Compression Molding: In this method, the neoprene rubber compound is placed into a heated mold cavity. The mold is then closed, and pressure is applied to shape the rubber. Compression molding is suitable for producing large, simple parts with consistent quality.
-
Injection Molding: This technique involves injecting the neoprene rubber compound into a mold cavity under high pressure. It allows for the production of complex and intricate parts with high precision. Injection molding is commonly used for manufacturing small to medium-sized rubber products.
-
Transfer Molding: Transfer molding combines elements of both compression and injection molding. The rubber compound is first heated and then transferred into a mold cavity under pressure. This method is used for producing parts with precise dimensions and surface finishes.
4. Curing (Vulcanization)
After molding, the neoprene rubber products undergo curing, also known as vulcanization. Curing involves heating the molded rubber in the presence of curing agents to initiate a chemical reaction that cross-links the rubber molecules. This process transforms the rubber from a soft, pliable material into a durable, elastic product with enhanced mechanical properties.
The curing process is typically carried out in a heated press or an oven, where the rubber is subjected to high temperatures and pressures for a specific duration. The result is a finished neoprene rubber product with improved strength, elasticity, and resistance to various environmental factors.
5. Quality Control and Testing
Before the neoprene rubber products are finalized for distribution, they undergo rigorous quality control and testing. This includes assessing properties such as tensile strength, elongation, hardness, and resistance to aging and chemicals. Quality control ensures that the products meet industry standards and perform effectively in their intended applications.
In summary, the manufacture of neoprene rubber products involves a detailed process of polymerization, compounding, molding, and curing. Each step is crucial in determining the final product's quality and performance. Neoprene rubber's unique properties, combined with advanced manufacturing techniques, make it a valuable material for a wide range of industrial and consumer applications.