Neoprene Rubber Parts Manufacturer
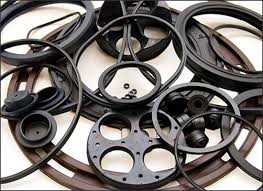
Contact : +91 97404 04503
Neoprene Rubber Parts Manufacturing: A Comprehensive Guide
Introduction to Neoprene Rubber Parts
Neoprene rubber, a versatile synthetic elastomer, is widely used in the manufacturing of various rubber parts due to its unique properties. Known for its durability, flexibility, and resistance to environmental factors, neoprene rubber is an excellent choice for applications that require resilience and longevity. This article delves into the key aspects of neoprene rubber parts manufacturing, highlighting why this material is favored across multiple industries.
Why Choose Neoprene Rubber?
Neoprene, also known as polychloroprene, is prized for its impressive range of benefits. It offers excellent resistance to ozone, weathering, and aging, making it ideal for outdoor and industrial applications. Additionally, neoprene is resistant to oil, chemicals, and heat, which enhances its suitability for demanding environments. The material maintains its flexibility and strength across a wide temperature range, making it a reliable choice for a diverse array of products.
Applications of Neoprene Rubber Parts
Neoprene rubber parts find applications in numerous sectors, including:
-
Automotive Industry: Neoprene is used for gaskets, seals, and bushings due to its resistance to oil and fuel. It provides a reliable seal and cushioning in various automotive components.
-
Industrial Equipment: The material is used in manufacturing vibration mounts, seals, and grommets, where its ability to withstand harsh conditions and reduce noise is crucial.
-
Consumer Goods: Neoprene's flexibility and comfort make it a popular choice for items like laptop sleeves, sports equipment, and wetsuits.
-
Construction: It is used for expansion joints, weather stripping, and insulation due to its durability and resistance to weathering.
Manufacturing Process of Neoprene Rubber Parts
The manufacturing process of neoprene rubber parts involves several key steps:
-
Compounding: The first step is to mix neoprene with various additives to enhance its properties. This includes curing agents, stabilizers, and fillers that improve strength, flexibility, and resistance.
-
Molding: Neoprene rubber is shaped using molding techniques. Compression molding and injection molding are commonly used to create precise and complex shapes. In compression molding, the neoprene mixture is placed in a mold cavity and subjected to heat and pressure. In injection molding, the material is injected into a mold under high pressure, allowing for high-volume production of intricate parts.
-
Curing: The molded parts are then cured through a process known as vulcanization. This involves heating the material to cross-link the polymer chains, which enhances the rubber's strength, elasticity, and durability.
-
Finishing: After curing, the parts are trimmed and finished to meet specific dimensions and tolerances. This may include surface treatment, such as grinding or polishing, to achieve the desired quality.
-
Quality Control: Rigorous quality control is essential to ensure that the neoprene rubber parts meet industry standards and specifications. This involves testing for physical properties, such as hardness, tensile strength, and elongation.
Benefits of Professional Manufacturing
Partnering with a professional neoprene rubber parts manufacturer offers several advantages:
-
Customization: Experienced manufacturers can tailor neoprene parts to specific requirements, ensuring that the product meets exact needs and performance criteria.
-
Consistency: Professional manufacturers use advanced technology and processes to ensure consistent quality and reliability across all products.
-
Expertise: Manufacturers with expertise in neoprene rubber can provide valuable insights and recommendations on material selection and design to optimize performance.
Conclusion
Neoprene rubber parts manufacturing is a critical industry that supports various applications across multiple sectors. The material’s outstanding properties—such as resistance to environmental factors and flexibility—make it a preferred choice for demanding applications. By understanding the manufacturing process and benefits of neoprene rubber, businesses can make informed decisions and partner with reliable manufacturers to meet their needs effectively. Whether for automotive, industrial, consumer goods, or construction applications, neoprene rubber parts offer unparalleled durability and performance.
This article is designed to provide a comprehensive overview of neoprene rubber parts manufacturing, optimized for SEO with relevant keywords and industry insights.