How Are Rubber Moulds Manufactured?
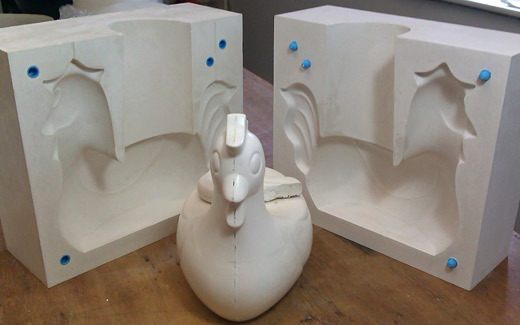
How Are Rubber Moulds Manufactured? – Framtas
Rubber Moulds Manufacturer in Bangalore
At Framtas, we specialize in precision-engineered rubber moulds used widely in the construction and industrial sectors. The manufacturing process of rubber moulds is both technical and quality-driven to ensure durability, flexibility, and a flawless finish for end products like paver blocks, tiles, and other concrete forms.
The process begins with high-grade rubber compound selection—typically polyurethane or silicone rubber—based on the desired hardness, temperature resistance, and flexibility. At Framtas, we use premium raw materials that ensure the moulds can withstand repeated use and harsh demoulding environments.
Next, CNC-machined master moulds or patterns are created with exact design specifications. These masters define the final shape, texture, and dimension of the mould. The selected rubber material is then heated and poured or injected into these masters through a compression or injection moulding process. This is done under controlled pressure and temperature to maintain uniformity.
After moulding, the rubber is allowed to cure—a process that sets its elasticity and strength. Once cooled, each mould undergoes precision trimming, finishing, and surface treatment to ensure smooth edges and detailed impressions. At Framtas, we perform quality checks at every stage, from dimension accuracy to surface finish.
To ensure customer satisfaction, we also offer custom rubber mould solutions tailored to unique designs and project requirements. Our moulds are tested for chemical resistance, flexibility, and longevity before delivery.
Whether you're in need of durable paver block rubber moulds, tile moulds, or decorative concrete moulds, Framtas delivers industry-leading solutions trusted across India.