High Quality Mold Making
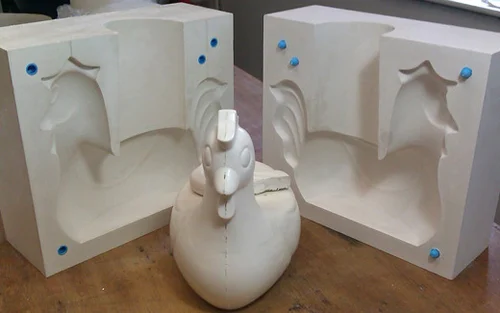
Contact : +91 97404 04503
High-quality mold making is a specialized process that forms the backbone of manufacturing a variety of products across multiple industries, including automotive, medical devices, consumer goods, and electronics. The quality of a mold directly impacts the functionality, precision, and appearance of the final product. Achieving a high standard in mold making requires an intricate combination of skills, technology, and materials.
The Basics of Mold Making
Mold making involves creating a cavity into which a liquid material—such as plastic, metal, or rubber—is poured and then allowed to cool or cure to form a solid part. The process begins with a design phase, where engineers use computer-aided design (CAD) software to create detailed 3D models of the part and the mold. This digital blueprint ensures that the final product meets precise specifications and tolerances.
Essential Materials
The material used for making molds depends on the end product's requirements. Common materials for molds include steel, aluminum, silicone, and epoxy resins. Steel molds are preferred for high-volume production due to their durability and resistance to wear, while aluminum molds are favored for prototype development or short production runs because they are easier to machine and more cost-effective. Silicone and epoxy are used for more intricate, flexible, or low-temperature applications.
High-Quality Mold Design Considerations
High-quality mold making starts with an impeccable design that accounts for factors such as shrinkage rates, draft angles, and parting lines. Shrinkage is a natural consequence of the cooling process, where materials contract slightly as they solidify. Accurately predicting this shrinkage is crucial to ensure that the final part meets dimensional specifications.
Draft angles are small, tapered inclines added to the vertical walls of the mold to facilitate easier removal of the molded part. Incorporating draft angles reduces the risk of damage during demolding and extends the mold's lifespan. Parting lines, which denote where the two halves of a mold come together, need to be strategically placed to minimize visible marks and ensure seamless assembly.
Advanced Technology in Mold Making
Modern mold making relies heavily on technology. CNC (computer numerical control) machining, electrical discharge machining (EDM), and 3D printing are essential tools in high-quality mold fabrication. CNC machining allows for precise cutting and shaping of mold materials, achieving exact dimensions and complex geometries. EDM is particularly useful for creating detailed patterns and working with hard metals. Meanwhile, 3D printing has revolutionized prototyping by providing rapid, cost-effective methods to create intricate mold designs and test them before committing to full-scale production.
Quality Assurance and Testing
Ensuring the mold's quality involves multiple stages of testing and validation. Dimensional checks using coordinate measuring machines (CMM) are critical for verifying that the mold conforms to design specifications. Additionally, trial runs are conducted to test how the mold performs under actual production conditions. These trials reveal any potential issues, such as poor filling, air entrapment, or uneven cooling, that could affect the quality of the final product.
Benefits of High-Quality Mold Making
The primary advantage of investing in high-quality mold making is the reliability and longevity of the mold, which can yield thousands to millions of parts with minimal degradation. A well-crafted mold minimizes defects such as warping, flash, and sink marks in the final products. This not only ensures customer satisfaction but also reduces production waste and costs in the long run.
Continuous Improvements and Industry Trends
The mold-making industry continues to evolve, with new materials and technologies emerging regularly. High-performance alloys and composite materials are being developed to extend mold life and improve product consistency. Automation, robotics, and artificial intelligence are also being integrated into the mold-making process to enhance precision and reduce production times.
In conclusion, high-quality mold making is a critical, detail-oriented process that relies on advanced engineering, premium materials, and cutting-edge technology. By focusing on meticulous design, precise fabrication, thorough testing, and continuous innovation, manufacturers can produce molds that enable efficient, high-quality production for a wide range of products.