EPDM Rubber Products Manufacturers
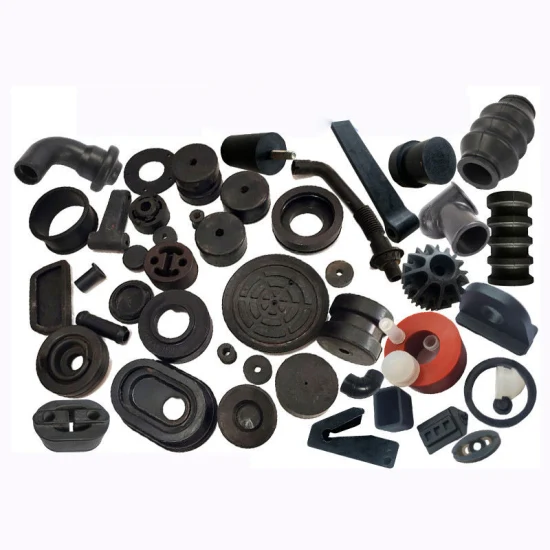
EPDM Rubber Products Manufacture
EPDM (Ethylene Propylene Diene Monomer) rubber is a type of synthetic rubber renowned for its excellent performance characteristics, including resistance to heat, ozone, weathering, and aging. Its versatile properties make it a popular choice in various applications, from automotive seals to roofing membranes and industrial gaskets. The manufacture of EPDM rubber products involves several key processes, each crucial in ensuring the material's performance and durability.
1. Raw Material Preparation
The manufacturing process begins with the preparation of raw materials. EPDM rubber is produced through the polymerization of ethylene, propylene, and a diene monomer. The quality of the final product depends significantly on the quality of these raw materials. Ethylene and propylene are derived from petrochemical sources, while the diene monomer (usually ethylidene norbornene or 1,4-hexadiene) is added to create cross-linkable structures within the rubber.
2. Mixing and Compounding
The next stage is the mixing and compounding of the EPDM rubber. In this step, the base EPDM polymer is blended with various additives to achieve desired properties. These additives include fillers (such as carbon black or silica) to enhance mechanical strength, plasticizers to improve flexibility, antioxidants to prevent degradation, and vulcanizing agents to promote cross-linking. The compounding process is carried out in high-shear mixers or internal mixers, where the ingredients are thoroughly blended to create a homogenous rubber compound.
3. Extrusion and Molding
Once the EPDM compound is prepared, it is shaped into products through extrusion or molding. Extrusion involves forcing the rubber through a die to produce continuous shapes, such as seals, gaskets, or profiles. The extruded rubber is then cut to length and cured. Molding, on the other hand, involves placing the rubber compound into a mold and applying heat and pressure to shape it into specific forms, such as automotive weather stripping or roofing tiles.
4. Vulcanization
Vulcanization is a crucial process that involves curing the rubber to enhance its physical properties. During vulcanization, the rubber compound is heated with sulfur or other cross-linking agents. This process creates cross-links between the polymer chains, improving the rubber's strength, elasticity, and resistance to environmental factors. The vulcanization process can be carried out in molds or in a continuous curing system, depending on the type of product being manufactured.
5. Quality Control
Quality control is an integral part of the manufacturing process. Throughout production, samples of the EPDM rubber are tested to ensure they meet the required specifications. Tests may include measurements of physical properties (such as tensile strength, elongation, and hardness), as well as assessments of aging, weather resistance, and chemical compatibility. Quality control ensures that the final products are consistent and reliable, meeting the performance standards expected by customers.
6. Post-Processing and Finishing
After vulcanization, the EPDM rubber products undergo post-processing to remove any imperfections and ensure proper finishing. This may include trimming excess material, surface treatments, and additional testing. The products are then packaged and prepared for distribution.
7. Applications
EPDM rubber products find applications across various industries. In the automotive sector, they are used for weather stripping, seals, and hoses. In construction, EPDM is used for roofing membranes and sealing materials. Industrial applications include gaskets, vibration dampers, and electrical insulation.
The manufacture of EPDM rubber products involves a meticulous process of material preparation, mixing, shaping, curing, and quality control. Each step is designed to ensure that the final products meet high standards of performance and durability, making EPDM a valuable material in a wide range of applications.