Die Making Factory
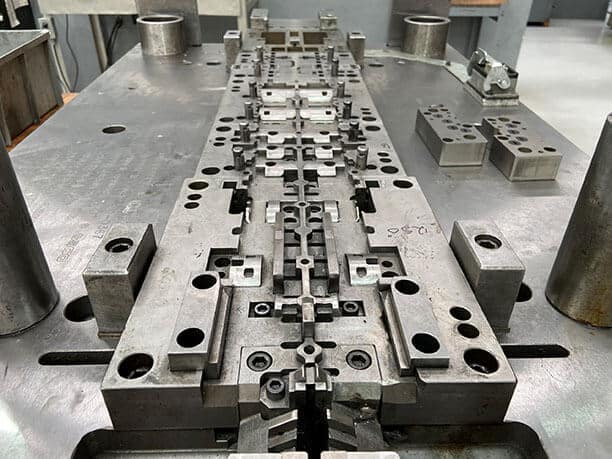
Contact : +91 97404 04503
Die Making Factory
A die making factory plays a crucial role in the manufacturing industry, providing the tools and components necessary for the production of a wide range of products. Dies are specialized tools used to shape or cut materials, primarily metals and plastics, into specific forms during the manufacturing process. The importance of die making cannot be overstated, as it directly influences the quality, efficiency, and cost-effectiveness of production.
Understanding Die Making
Die making involves the design, fabrication, and testing of dies. The process typically starts with the design phase, where engineers create detailed blueprints using advanced computer-aided design (CAD) software. These designs must consider various factors, such as the material to be used, the desired dimensions, and the production methods.
Once the design is finalized, the fabrication process begins. This phase requires a combination of precision machining, skilled craftsmanship, and advanced technology. Materials commonly used in die making include high-carbon steel, aluminum, and specialty alloys, chosen for their durability and resistance to wear. The manufacturing process involves several steps, including cutting, grinding, and assembly, to ensure that the dies meet the stringent quality standards required for efficient production.
Types of Dies
There are several types of dies produced in a die making factory, including:
-
Stamping Dies: Used for shaping and cutting metal sheets in various industries, such as automotive and electronics.
-
Injection Molding Dies: Essential for producing plastic parts by injecting molten plastic into a mold.
-
Progressive Dies: These allow for multiple operations to be performed in a single pass, improving efficiency and reducing production time.
-
Extrusion Dies: Used in the extrusion process to create continuous shapes, such as pipes or profiles, from various materials.
The Die Making Process
-
Design and Prototyping: The first step involves conceptualizing the die based on product specifications. Prototyping may be performed to test designs before full-scale production.
-
Material Selection: The choice of material for the die is critical, as it impacts the die’s lifespan and performance. Factors like tensile strength, hardness, and thermal stability are taken into account.
-
Machining: High-precision machines, such as CNC milling machines and wire EDM (Electrical Discharge Machining), are utilized to create the die’s intricate features.
-
Assembly and Testing: Once machined, the components of the die are assembled. Rigorous testing follows to ensure that the die performs as intended under actual manufacturing conditions.
-
Maintenance and Repair: A die making factory also offers maintenance services to extend the life of the dies and ensure they operate at peak efficiency.
Quality Control and Standards
Quality control is a fundamental aspect of die making. Factories adhere to strict industry standards and utilize advanced inspection techniques, such as coordinate measuring machines (CMM) and laser scanning, to ensure that every die produced meets the required specifications. This commitment to quality helps manufacturers avoid costly production delays and defects.
Conclusion
In conclusion, a die making factory is essential to the manufacturing landscape, providing critical tools that shape the production processes across various industries. The combination of skilled craftsmanship, advanced technology, and stringent quality control ensures that the dies produced are reliable, efficient, and tailored to meet the diverse needs of manufacturers. As industries continue to evolve and innovate, the role of die making will remain integral to maintaining high standards of production quality and efficiency.