All Tool Work Manufacturer Bangalore
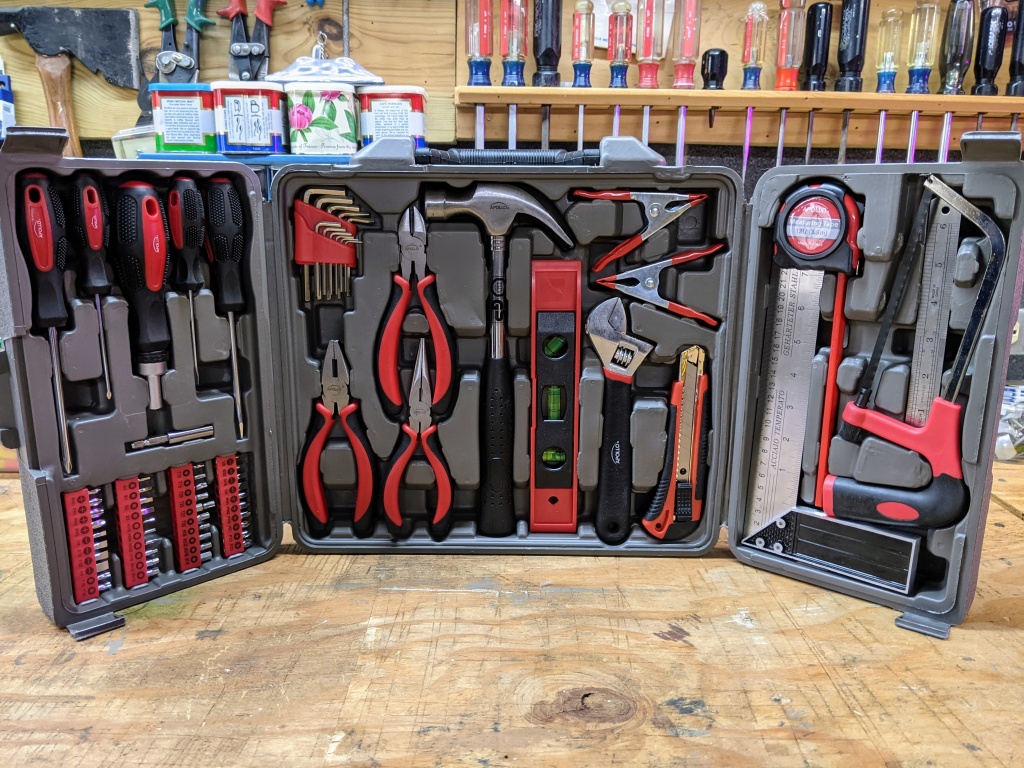
Contact : +91 97404 04503
Tool manufacturing encompasses the production of various tools essential for a wide range of applications, from industrial machinery to hand-held instruments. This process involves several techniques, materials, and technologies, each tailored to create tools that meet specific functional requirements and industry standards.
1. Materials Used in Tool Manufacturing
The choice of materials is crucial in tool manufacturing, as they determine the tool's durability, strength, and performance. Common materials include:
- Steel: High-carbon steel is often used for cutting tools due to its hardness and ability to retain sharp edges. Stainless steel offers corrosion resistance, making it suitable for tools exposed to moisture.
- Carbide: Tungsten carbide is a popular material for cutting tools and inserts due to its exceptional hardness and wear resistance.
- Ceramics: Ceramic tools are known for their high wear resistance and ability to operate at elevated temperatures.
- Plastics and Composites: Used for non-cutting tools, these materials are lightweight and resistant to corrosion.
2. Manufacturing Techniques
The manufacturing of tools involves various techniques, including:
-
Casting: Metal casting involves pouring molten metal into a mold. This technique is suitable for producing complex shapes, such as tool bodies or handles. Common casting methods include sand casting, investment casting, and die casting.
-
Machining: This subtractive manufacturing process includes techniques like turning, milling, drilling, and grinding. Machining allows for precise dimensions and surface finishes, making it ideal for creating intricate parts and cutting tools.
-
Forging: In forging, metal is heated and shaped using compressive forces. This process enhances the material's mechanical properties and is commonly used for producing high-strength components like tool heads and striking tools.
-
Heat Treatment: To enhance the hardness and toughness of tools, heat treatment processes such as quenching and tempering are employed. This ensures that tools can withstand the stresses of daily use.
-
Coating: Surface coatings, such as TiN (Titanium Nitride) or diamond-like carbon (DLC), are applied to tools to improve their wear resistance, reduce friction, and enhance performance.
3. Quality Control
Quality control is vital in tool manufacturing. This involves rigorous testing and inspection of tools at various stages of production. Techniques like dimensional analysis, hardness testing, and surface finish evaluation ensure that tools meet industry standards and customer expectations.
4. Innovations in Tool Manufacturing
With advancements in technology, tool manufacturing has seen significant innovations:
-
CNC Machining: Computer Numerical Control (CNC) machines allow for high precision and repeatability in manufacturing. CNC technology is widely used for cutting, milling, and engraving tools.
-
3D Printing: Additive manufacturing is gaining traction in tool production, enabling the creation of complex geometries that traditional methods cannot achieve. This technique is particularly useful for prototyping and small-scale production.
-
Smart Tools: Integration of IoT (Internet of Things) technology in tools allows for real-time monitoring of tool performance and condition, leading to improved maintenance and efficiency.
5. Sustainability Practices
As environmental concerns grow, tool manufacturers are increasingly adopting sustainable practices. This includes using recycled materials, reducing waste during production, and implementing energy-efficient processes.
Conclusion
Tool manufacturing is a multifaceted process that combines traditional craftsmanship with modern technology. The choice of materials, manufacturing techniques, and innovative practices play a crucial role in producing high-quality tools that meet the demands of various industries. As technology continues to evolve, the future of tool manufacturing promises even greater advancements in efficiency, performance, and sustainability.